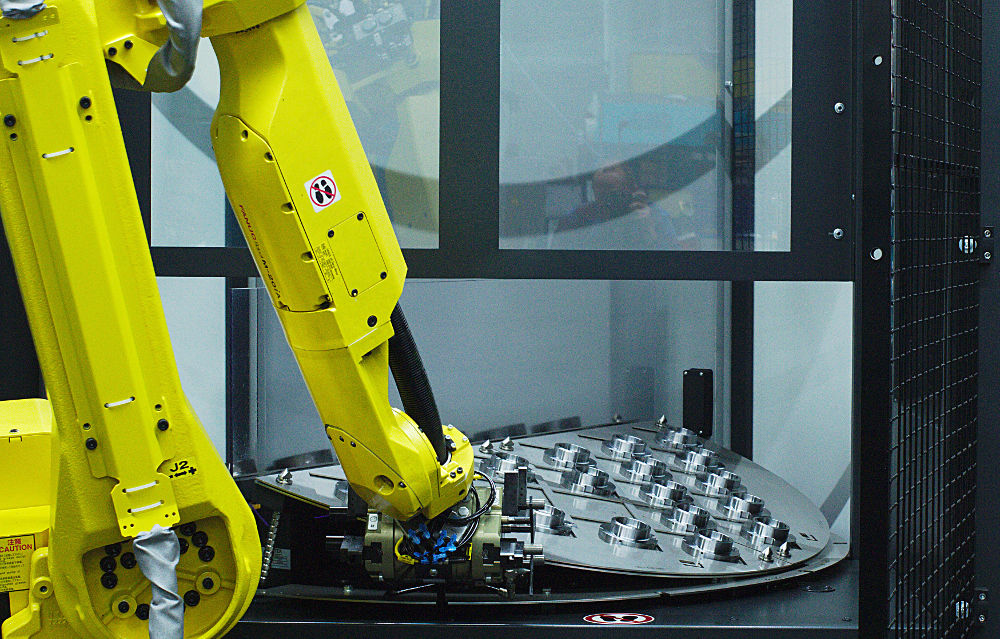
Mit einer gleichsam offenen wie flexiblen Automationslösung für zwei CNC-Dreh-Fräszentren erzielte der Systemanbieter KEB Automation bereits nach kurzer Zeit eine Produktivitätssteigerung von rund 30 Prozent pro Schicht. Ein erstes positives Fazit eines Pilotprojekts, in dem weiterhin wertvolle Erfahrungen gesammelt werden. Doch von Anfang an.
1972 mit sechs Mitarbeitern gegründet, hat sich die KEB Automation KG zu einem weltweit agierenden mittelständischen Unternehmen entwickelt. „Wir produzieren das komplette Portfolio für die Antriebstechnik, von der Steuerung bis hin zur Welle“, erklärt Hartmut Lippert, Betriebsleiter Magnettechnik und Prokurist von KEB.
Weltweit beschäftigt die KEB-Gruppe rund 1.400 Mitarbeiter verteilt auf fünf Produktionsstandorte, darunter zirka 900 Mitarbeiter in zwei Werken am Firmenhauptsitz in Barntrup (NRW, Kreis Lippe).
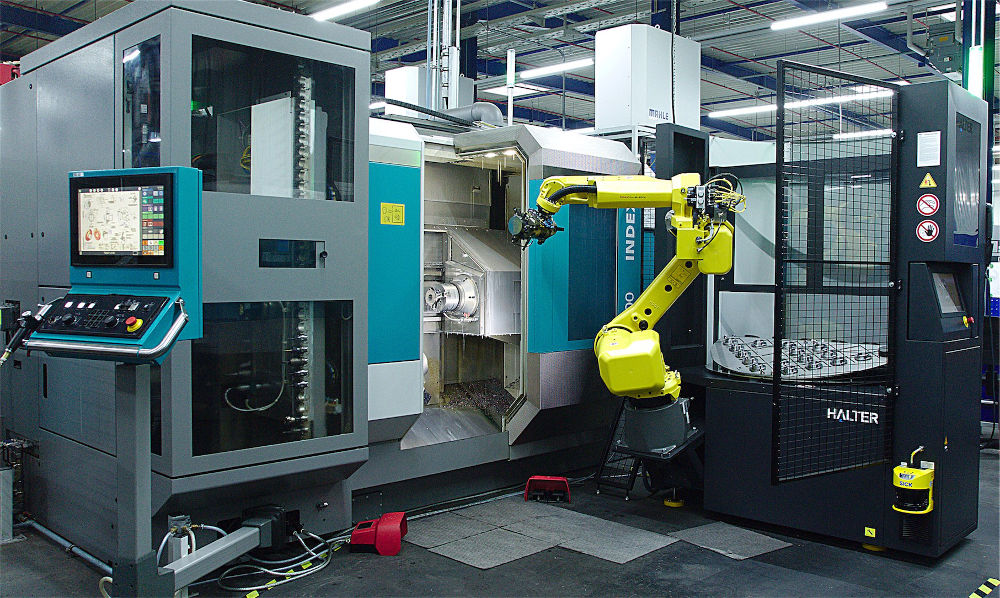
Kontinuierliche Modernisierung
Im Werk 1 wird die elektronische Antriebstechnik produziert, also bspw. Steuerungen, Frequenzumrichter, Servosteller etc. In Werk 2, das seine Produktion im Jahr 2000 aufnahm, befindet sich die Fertigung der mechanischen Antriebstechnik und Magnettechnik. Das Leistungsspektrum reicht hierbei von der Konstruktion bis zum fertigen Produkt, wobei hinter jeder Lösung zumeist eine individuelle Engineering-Leistung steht. Die Losgrößen bewegen sich dementsprechend zwischen Stückzahl 1 bis hin zu mehreren tausend Werkstücke bspw. für den Automotive-Bereich. Nach Aussagen von Hartmut Lippert unterscheide sich die KEB von seinen Wettbewerbern vor allem durch die hohe Fertigungstiefe. Der Betriebsleiter präzisiert: „60 Prozent aller Zerspanungsteile kaufen wir zu. 40 Prozent werden von uns selbst gefertigt, insbesondere Werkstücke, für die spezielles Know-how erforderlich ist.“
Die Zerspanung im Werk 2 deckt daher mit aktuell zirka 50 Maschinen das komplette CNC-Bearbeitungsspektrum ab. „Die ersten Maschinen kamen ursprünglich aus dem Werk 1, wurden aber mit dem Ziel einer höheren Produktivität von Beginn an sukzessive durch leistungsfähigere Lösungen ersetzt und zusätzlich der Maschinenpark aufgestockt“, berichtet Uwe Rauchschwalbe, Abteilungsleiter Zerspanung, Produktion Magnettechnik.
Konkrete Anforderungen an die Automation
In diesem Sinne investierte die KEB in den letzten beiden Jahren u.a. in zwei hochleistungsfähige CNC-Dreh-Fräszentren R200 von Index, die mit einer 5-Achsbearbeitung und Gegenspindel für sich genommen schon eine sehr hohe Teilevielfalt und Produktivität ermöglichen. „Wir haben die beiden Maschinen für die Bedienung von einem Werker gegenüberliegend installiert. Von Anfang an stand für uns außerdem fest, dass wir die Be- und Entladung beider Maschinen automatisieren wollten“, so Lippert.
Der Standort der Maschinen sollte zu diesem Zweck beibehalten werden, sodass sich die Automationslösung nicht nur in die gegebenen Platzverhältnisse einpassen musste, sondern bei Bedarf auch die Be- und Entladung beider Maschinen übernehmen kann. „Zudem wollten wir eine offene Lösung, da im Falle einer Roboterzelle ein Schutzzaun die Zugänglichkeit zu den Maschinen erschwert hätte. Eine zentrale Forderung galt der Flexibilität, da wir beabsichtigten, auf beiden Maschinen eventuell auch Null-Serien und kleinere Stückzahlen zu fertigen“, betont Lippert.
Automatische Be- und Entladung nicht nur für rotationssymetrische Teile
Mehrere Automationslösungen wurden in Augenschein genommen, darunter auch ein Portalsystem. Letztendlich fiel die Entscheidung für einen HALTER LoadAssistant Universal. Hartmut Lippert: „Dieses System erfüllte alle unsere Anforderungen und ermöglicht es uns u.a., ein neues Teil an einer Maschine zu rüsten, noch während die vorherigen Teile abgearbeitet werden.“
Der 6-achsige Fanuc-Roboter des HALTER LoadAssistant versorgt momentan eine Maschine über ein rotierendes Be- und Entladesystem als Teilepuffer. Dieser Puffer kann über insgesamt sieben verschiedene Rasterplatten Werkstücke mit Durchmessern von 10 bis 230 mm aufnehmen. „Für rotationssymetrische Teile verwenden vor allem die Rasterplatte für Teiledurchmesser von 23 bis 100 mm mit einer Gesamtkapazität von 40 Werkstücken. Darüber hinaus fertigen wir auch nicht-rotationssymetrische Teile. Hierzu hat Halter CNC Automation, der Hersteller der Roboterzelle, eigens eine Rasterplatte anfertigen lassen, die über ein Fassungsvermögen von insgesamt 68 Teile verfügt“, erklärt Uwe Rauchschwalbe.
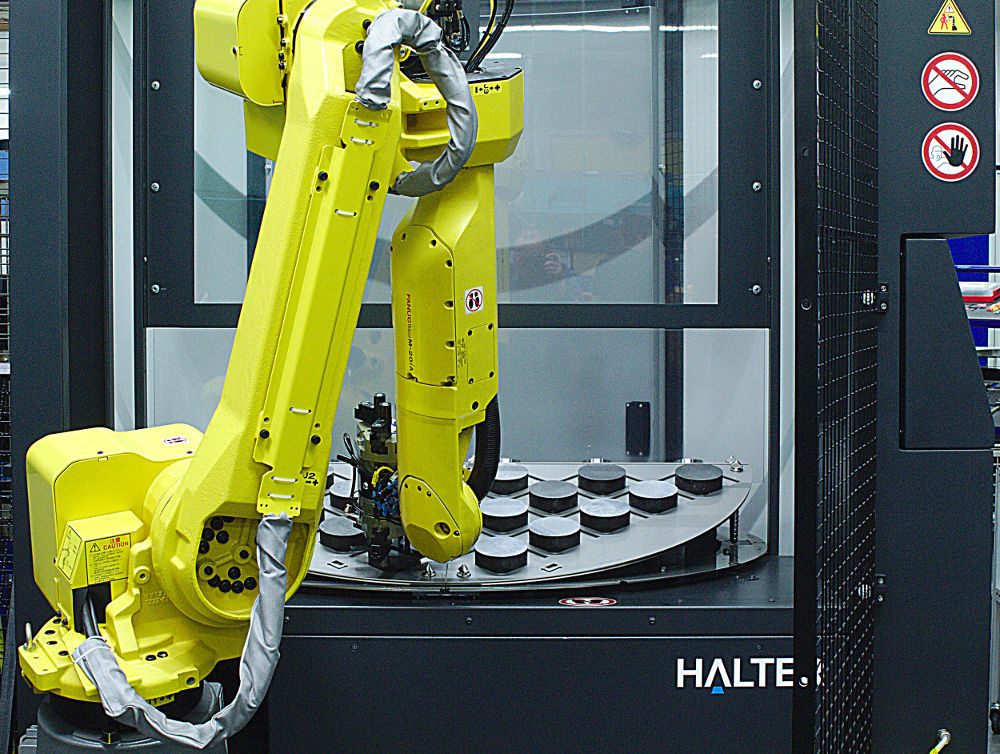
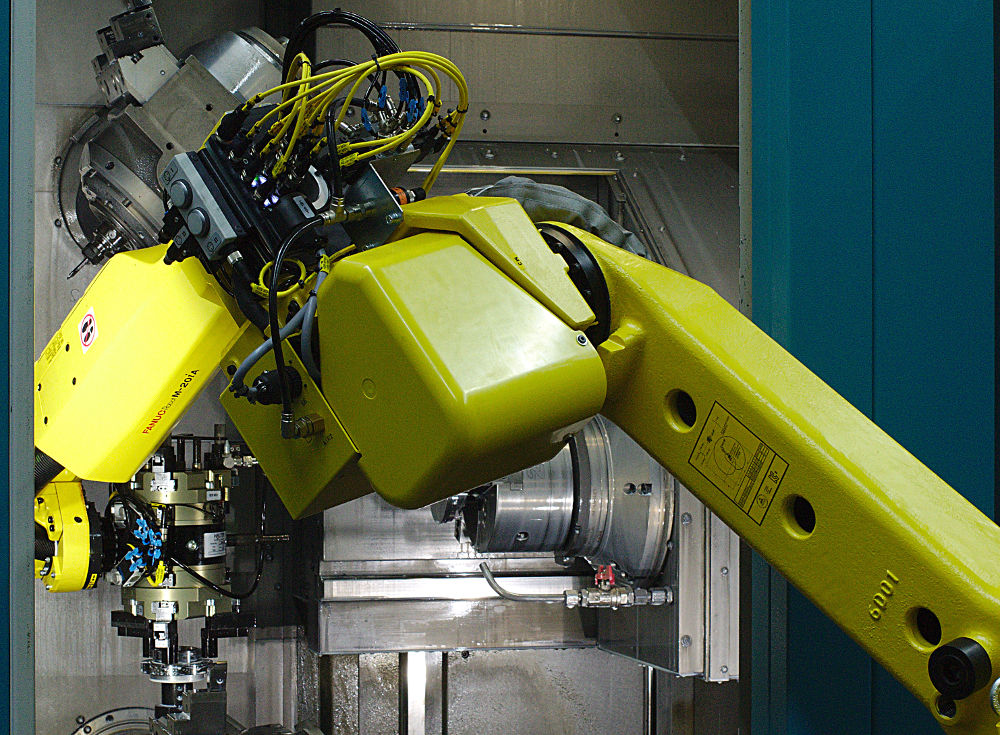
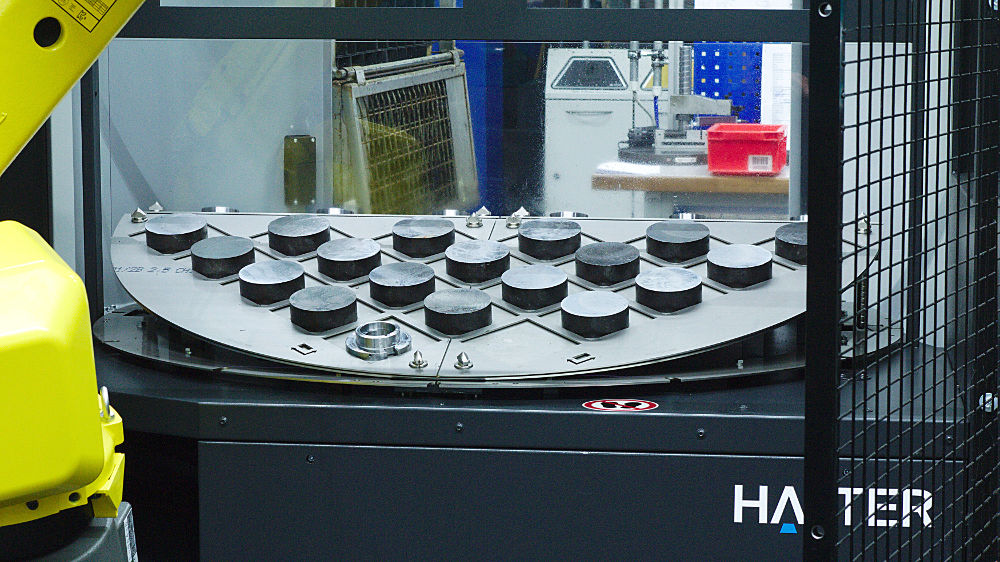
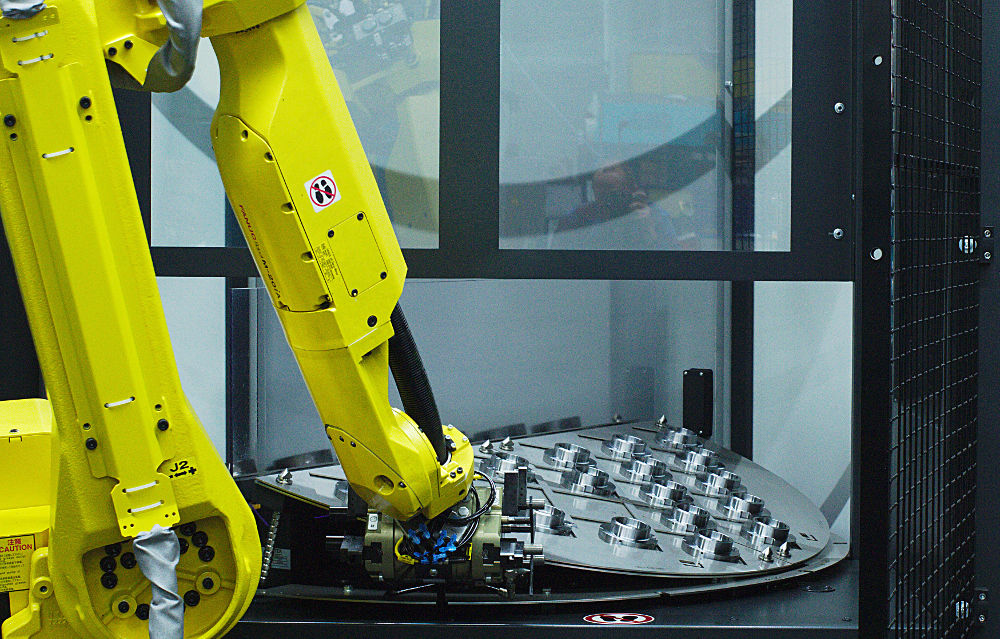
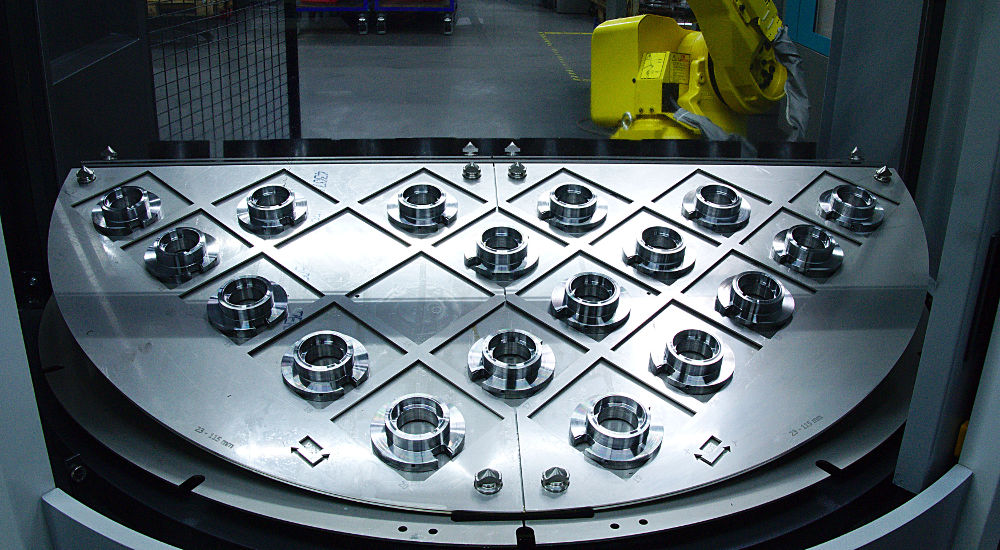
Hohe Spindellaufzeiten durch autonome Fertigung
Beide Index R200 sind für die Automation mit dem HALTER LoadAssistant vorbereitet, sodass in Kürze damit begonnen werden kann, auch das zweite CNC-Dreh-Fräszentrum mit dem System zu be- und entladen. „Die Losgrößen an der aktuell automatisierten Maschine bewegen sich zwischen 20 und 2.000 Stück. Momentan produzieren wir Bauteile, für deren komplette Produktion wir rund fünf bis sechs Wochen benötigen, wobei wir pro Woche zirka 1.700 Teile fertigen. Durch die Automation können wir hierbei die Produktion in Pausen, neue Schichten und ins Wochenende hineinlaufen lassen. So erreichen wir hohe Spindellaufzeiten mithin eine hohe Produktivität“, meint Uwe Rauchschwalbe und Hartmut Lippert ergänzt: „Unser Ziel ist eine automatisierte und vor allem prozesssichere Produktion in einer komplett mannlosen Schicht. Aber das hängt natürlich von der jeweiligen Bearbeitungszeit der Werkstücke ab. Bei den nicht-rotationssymetrischen Teilen haben wir bspw. eine Bearbeitungszeit von fast vier Minuten. Die Index R200 kann daher mit einer Rasterplatte für 68 Teile im Zusammenspiel mit dem HALTER LoadAssistant knapp fünf Stunden autonom arbeiten. Das ist schon ein sehr gutes Ergebnis.“
Konkrete Auswirkungen auf die Maschinenperipherie
Seit Inbetriebnahme der Automationslösung Mitte Juli 2017 hat man bereits eine Vielzahl an Erfahrungen gesammelt, darunter die wichtige Erkenntnis, dass sich bei dem Einsatz eines solchen Systems die Peripherie um die Maschine ändern muss, wie Betriebsleiter Lippert verdeutlicht: „So haben wir derzeit etliche Tätigkeiten aus der Maschine ausgelagert, da durch die Automation Nebenzeiten frei werden, in denen der Werker z. B. Mess- und Prüfaufgaben übernimmt, während produziert wird. Bei einer völlig autonomen Fertigung müssen solche Aufgaben integraler Bestandteil der Maschine oder eine Tätigkeit des Roboters sein, um prozesssicher zu produzieren. Zusätzlich sollte, etwa über den Roboter, eine automatische Reinigung der Spannmittel und der Fertigteile erfolgen, damit diese frei von Spänen sind. In einer vollautomatisierten Produktion werden derartige Aufgaben wohl zu gleichen Teilen von der Maschine und vom Roboter übernommen. Einer unserer nächsten Schritte wird es daher bspw. sein, kabellose Messtaster im Arbeitsraum der beiden Maschinen zu installieren, um nach Vorgabe kritische Baumaße automatisch zu vermessen und bei Bedarf entsprechende Korrekturparameter an die Maschinensteuerung zu übergeben.“
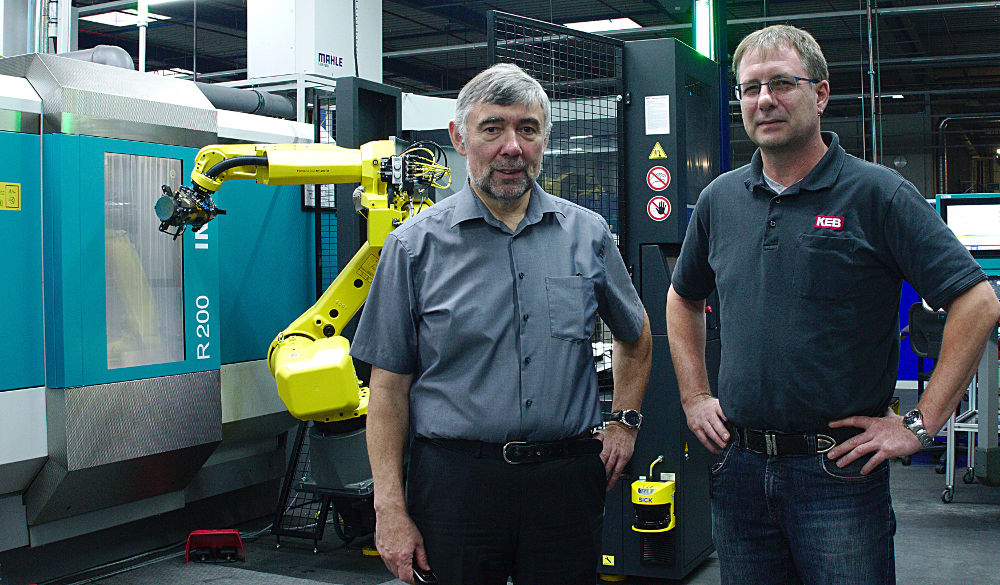
Realistische Ergebnisse
Hartmut Lippert und Uwe Rauchschwalbe betrachten die aktuelle Automation der CNC-Dreh-Fräszentren mit dem HALTER LoadAssistant als ein Pilotprojekt, in dem weiterhin wertvolle Erfahrungen gesammelt werden und auch durchaus nicht alles reibungslos verläuft: „Ein Problem bei der Anbindung solcher Automationssysteme ist, dass es keine standardisierte Schnittstellen gibt. Es wäre daher wünschenswert, dass sowohl Anbieter von Automationslösungen als auch Maschinenhersteller in diesem Bereich zukünftig stärker miteinander kooperieren, um gewisse Standards für die bidirektionale Kommunikation zu definieren. Ansonsten bleibt die Schnittstellenproblematik zunächst beim Anwender, der dann gemeinsam mit einem Maschinenhersteller und einem Anbieter von Automationssystemen Lösungen finden muss“, betont Hartmut Lippert, der dennoch mit dem bisherigen Verlauf des Projektes zufrieden ist: „Da wir momentan nur eine der beiden Index R200 automatisiert haben, können wir die Ergebnisse hinsichtlich eines Produktivitätsgewinns sehr gut vergleichen – und der ist offensichtlich. Bei der Bearbeitung rotationssymetrischer Teile ohne automatische Be- und Entladung erreichen wir Stückzahlen von zirka 90 bis 100 pro Schicht. Mit dem HALTER LoadAssistant sind es indes rund 130 Teile pro Schicht. Das bedeutet eine Produktivitätssteigerung von rund 25 bis 30 Prozent pro Schicht, und das zu einem Zeitpunkt, zu dem wir weitere Maßnahmen für einen noch höheren Grad der autonomen Fertigung an den Index R200 noch nicht konkret umgesetzt haben.“
Über KEB Automation:
Systemanbieter rund um die Antriebstechnik
Vor rund 45 Jahren gegründet, hat sich die KEB Automation zu einem weltweit agierenden mittelständischen Unternehmen entwickelt. Weltweit beschäftigt das in zweiter Familiengeneration inhabergeführte Unternehmen rund 1.400 Mitarbeiter verteilt auf vier Produktionsstandorte in den U.S.A., Japan, China (Shanghai) und Deutschland. Rund 900 Beschäftigte arbeiten am Hauptsitz in Barntrup. Darüber hinaus produzieren etwa 160 Mitarbeiter im sächsischen Schneeberg die Getriebe für die Antriebslösungen der KEB. Die Kunden des Systemanbieters kommen aus den unterschiedlichsten Branchen, z. B. Medizintechnik, Windenergie, Maschinenbau oder der Bereich Automotive, um nur einige Beispiele zu nennen. Die KEB Gruppe erzielte im Jahr 2016 einen Umsatz von zirka 210 Mio. Euro.
© Martinus Menne, 2017. Erschienen in MM Maschinenmarkt