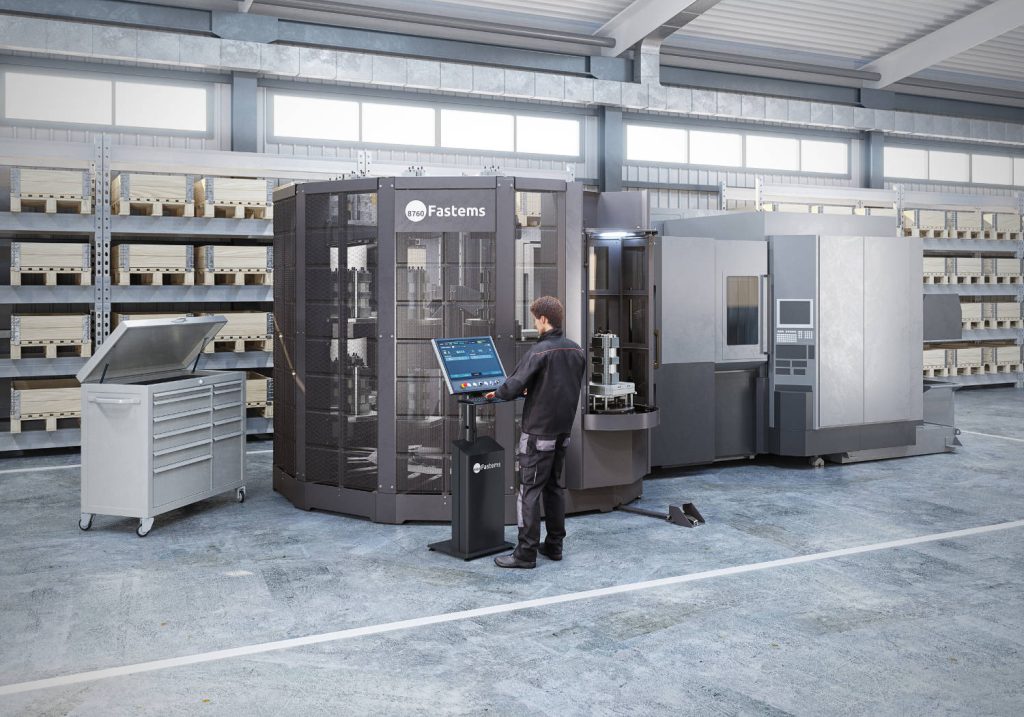
In einem „Formel-1-Projekt“ möchte Cutmetall Recycling Tools Germany binnen kürzester Zeit möglichst viele wertvolle Erkenntnisse zum Thema Automatisierung sammeln. Die wichtigsten Partner: Fastems, Heller und Haimer.
Download Reportage (hochauflösende Bilder auf Anfrage)
Ziel des Projektes ist es, neue Standards und Abläufe zu erproben sowie Programme und Vorrichtungen zu erstellen, um sie 2025 in einer großen Gesamtlösung von Fastems unmittelbar anwenden zu können. Damit wird eine ideale Vorarbeit für eine rasche und risikoarme Inbetriebnahme der Großanlage geleistet.
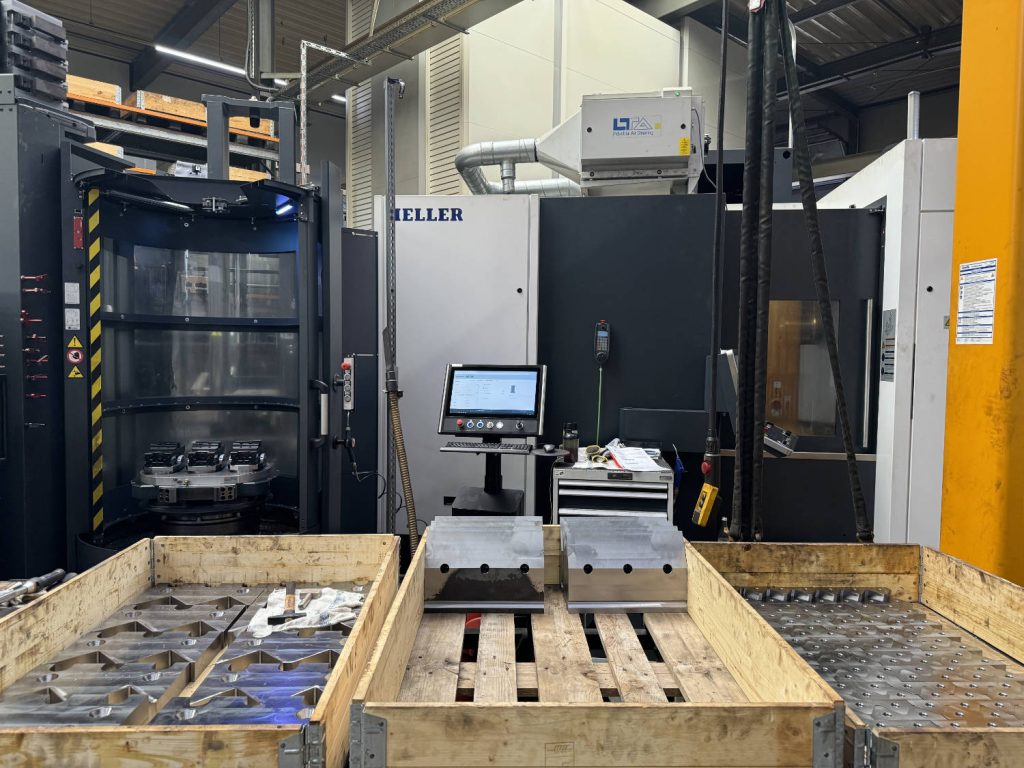
Cutmetall Recycling Tools Germany mit Sitz in Eisfeld (Thüringen) gehört zur Cutmetall-Unternehmensgruppe und produziert als OEM mit rund 40 Mitarbeitern Verschleiß- und Ersatzteile für die Recyclingindustrie. „Wir stellen Lose von 1 bis 20.000 her, wobei sich die durchschnittlichen Losgrößen jedoch zwischen 20 und 200 Stück bewegen“, sagt Geschäftsführer Florian Fischer.
Geld verdient wird nur mit Spindelstunden
Wer den Mann kennt weiß, dass er eine ganz eigene Sicht auf das Thema Automatisierung hat, die z. B. deutlich wird, wenn er den Automatisierungsgrad in seinem Betrieb vor dem F1-Projekt beurteilen soll: „Das hängt immer davon ab, was sie unter Automatisierungsgrad verstehen. Wir haben 12 CNC-Maschinen, ein Sägezentrum und drei Roboter zum Be- und Entladen von Maschinen. Für viele ist das vielleicht schon High-End, für mich nicht. Hier findet im Sinne von Lean-Manufacturing nicht genügend Differenzierung zwischen Wertschöpfung und Verschwendung statt. Es geht bei der Automatisierung nicht darum, irgendetwas am Laufen zu halten, sondern möglichst viele Spindelstunden zu erzielen, denn damit verdienen wir unser Geld.“
Viele wertvolle Erfahrungen durch F1-Projekt
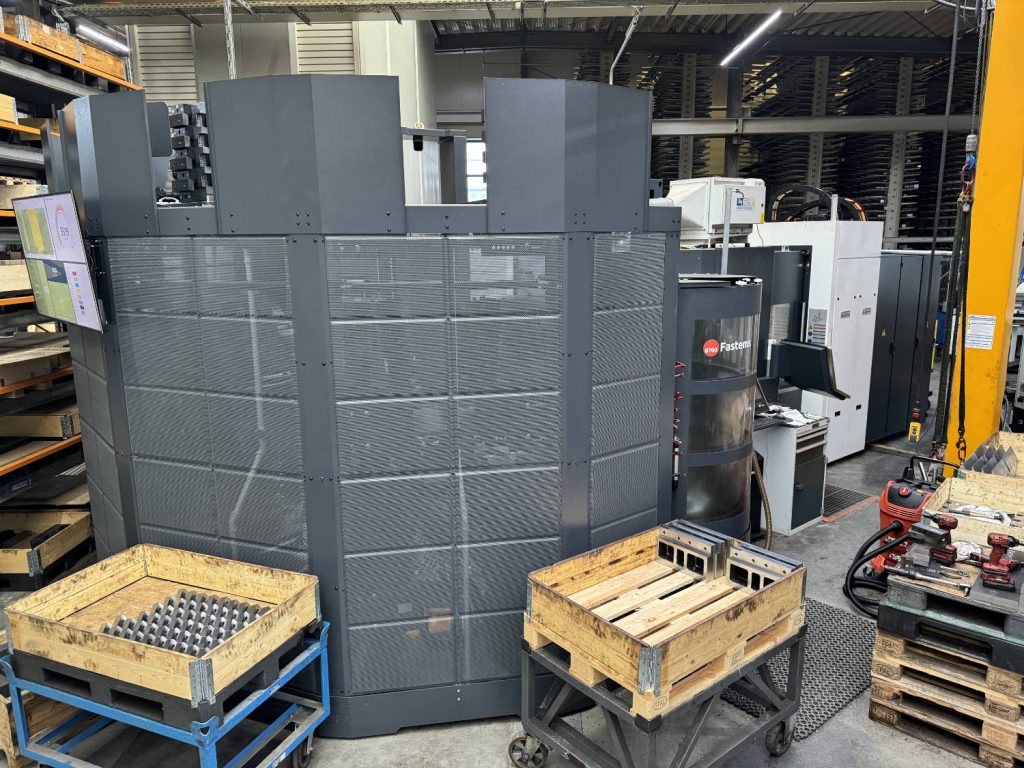
Die Verfügbarkeit von qualifizierten Mitarbeitern sei der stärkste Engpass in seinem Unternehmen so Fischer. „Wir haben überdies viel zu wenig Anlagen, die rund um die Uhr produzieren können und hatten außerdem bislang keine einzige Horizontal-Fräsmaschine. Bereits an vertikalen Fräsmaschinen ist die Späneabfuhr der größte Flaschenhals, sodass nicht rund um die Uhr automatisiert produziert werden kann, zumal uns bis dato auch genügend große Werkzeugspeicher fehlten.“
Um die Situation in seinem Unternehmen zu verändern, starteten der Gesellschafter Oliver Huther und Fischer das F1-Projekt, auch im Hinblick auf eine zukünftig geplante ehrgeizige Automatisierung mit einem Multilevel-System (MLS) von Fastems zur Verkettung von mehreren CNC-Maschinen in einem flexiblen Fertigungssystem. Das Ziel: Mit einer überschaubaren Lösung binnen kürzester Zeit möglichst viele wertvolle Erfahrungen zur Automatisierung zu sammeln.
Standards bilden Basis für mehr Produktivität
Flankierend hierzu entschloss sich Cutmetall Recycling Tools Germany nach entsprechender Vorplanung zur konsequenten Einführung mehrerer Produktionsstandards.
So soll zukünftig nur noch in Werkzeugmaschinen mit der Steuerung eines Herstellers und Palettenwechsler sowie einheitlichem Spannfutter investiert werden. In der Produktion kommen nur noch horizontale Fräsmaschinen mit automatisierter Späneabfuhr zum Einsatz. Die Standardisierung reicht bis hin zur automatisierten Aufbereitung des Kühl-/Schmiermittels für die Maschinen, um die Prozesse so stabil wie möglich zu halten. Florian Fischer beschreibt die zentralen Ziele: „Das gesamte Rüsten, Umrüsten und das gesamte Werkzeug- sowie Spänemanagement soll ausschließlich hauptzeitparallel erfolgen.“
Um sich verschiedenste Automatisierungslösungen anzuschauen, reiste der Geschäftsführer nach eigenen Angaben tausende von Kilometer: „Auch unter dem Aspekt, bereits im Ansatz die Fehler zu vermeiden, die andere womöglich schon gemacht haben.“
Sportliche Ziele für die Projektrealisierung
Im September 2022 hatte Cutmetall während der AMB erstmals Kontakt zur Gebr. Heller Maschinenfabrik und sah dort das horizontale 5-Achsbearbeitungszentrum HF 5500. Auf dem Stand von Fastems fand er mit einem Flexible Pallet Tower (FPT) schließlich die passende Automatisierung. „Wir haben wenig später quasi das Bearbeitungszentrum aus der laufenden Produktion von Heller gekauft und den ebenfalls kurzfristig verfügbaren FPT sowie ein Werkzeugvoreinstellgerät von Haimer bestellt, denn wir wollten das Gesamtsystem im April des Folgejahres gesamtvernetzt, produktiv einsetzen.“
Überzeugt hat Fischer vor allem das platzsparende Konzept des FPT-1000, das es ermöglicht, eine Vielzahl an Paletten auf kleinem Raum für die Automatisierung einer Werkzeugmaschine bereitzustellen. Der FPT-1000 ist für Nutzlasten bis 1.000 kg (inkl. Palette) und Palettengrößen von 500 x 500 mm bis 630 x 630 mm ausgelegt. Auf einer Stellfläche von nur 19 m2 kann der FPT insgesamt 12 bis 24 Paletten in zwei unterschiedlichen Höhen aufnehmen und ermöglicht damit eine hochproduktive auftragsbezogene Fertigung mit nur einer CNC-Maschine.
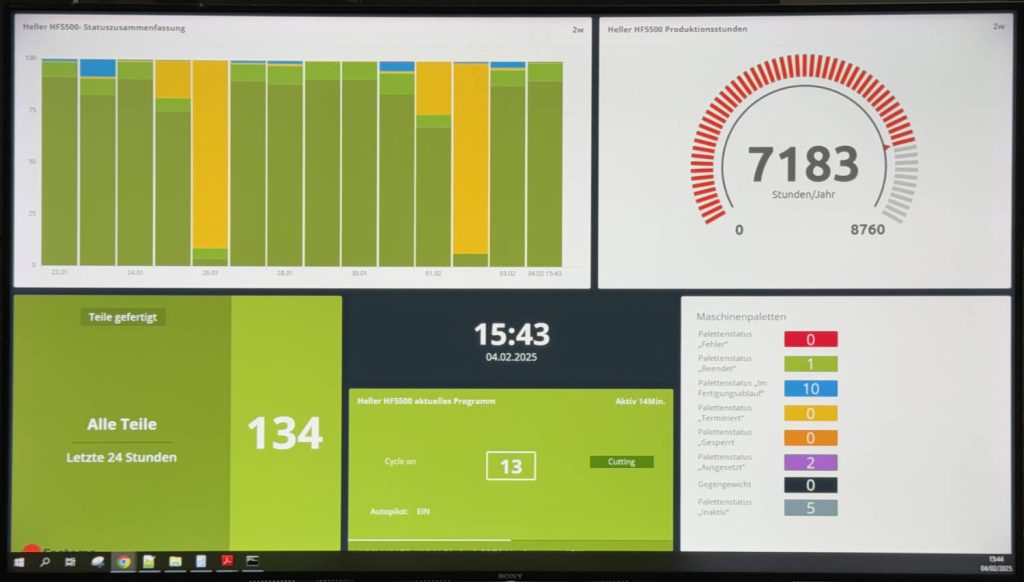
MMS von Fastems gab Ausschlag für Entscheidung
Entscheidend ist hierbei aus Sicht von Florian Fischer die Gesamtheit der Lösung, weil Maschine, Werkzeugvoreinstellung und Automatisierung zusammengeführt werden müssen. „Insbesondere die Software-Schnittstellen-Thematik zwischen diesen drei Gewerken ist für mich daher von zentraler Bedeutung, wobei die MMS von Fastems im Grunde das Entscheidungspendel in Richtung des FPT gelenkt hat.“
Die Manufacturing Management Software (MMS) von Fastems gehört derzeit wohl zu den fortschrittlichsten Steuerungen für die automatisierte Planung, Überwachung und Ausführung einer spanabhebenden Fertigung und kann die Produktion bis zu 96 Stunden im Voraus planen. Für den Geschäftsführer von Cutmetall Recycling Tools Germany besteht ein besonderer Vorteil der MMS darin, dass sie die Fertigungsressourcen in den Vordergrund stellt: „Die MMS prüft vor jedem Auftrag die hierfür notwendigen Ressourcen und startet die Fertigung erst, wenn diese bereitstehen, bspw. Rohmaterial, NC-Programme, Werkzeuge inklusive Prüfung der Werkzeugstandzeiten, Vorrichtungen, etc. Hierdurch werden auch die Workpieces in Process, also die Teile, die bislang normalerweise bis zum nächsten Bearbeitungsschritt in der Halle herumstanden, deutlich geringer.“
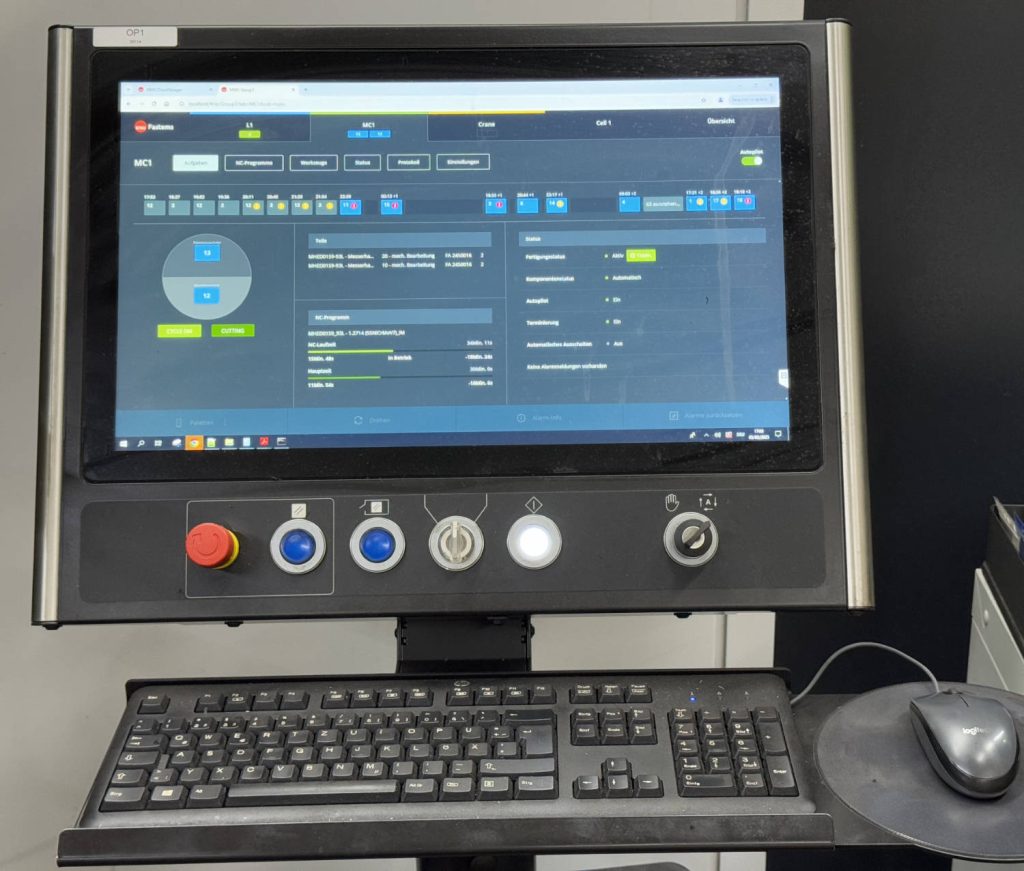
Zentrales Management aller Fertigungsressourcen
Einmal in der MMS hinterlegte Stammdaten für Aufträge lassen sich bei Wiederholaufträgen sofort abrufen, sodass die Produktion unmittelbar gestartet werden kann. „Das spart enorm viel Zeit, vorausgesetzt das Rohmaterial, die Paletten und die Werkzeuge stehen parat. Die MMS übernimmt in diesem Zusammenhang das vollständige Werkzeugmanagement und erteilt die entsprechenden Aufträge auch an die Werkzeugvoreinstellung. Die MMS managet somit zentral alle wichtigen Produktionsressourcen. Wer behauptet, Software mache noch keine Späne, hat Recht. Allerdings hilft die MMS entscheidend, die effektiven Spindelstunden zu erhöhen, denn jede Minute, die eine Maschine keine Späne macht, ist Verschwendung.“
Momentan werden die Aufträge noch manuell in die Steuerung eingegeben. Mit Blick auf weitere Automatisierungsprojekte und der damit verbundenen Anbindung der MMS an das ERP-System haben die rund 20 Mitarbeiter im F1-Team aber schon jetzt viel Gelegenheit, sich mit der Software und deren Potenzialen vertraut machen. Sie wissen daher genau, was zu tun ist und werden nach dem weiteren Ausbau der automatisierten Fertigung von Anfang an entsprechende Kenntnisse haben.
FPT-1000 hält Fertigteile im stetigen Fluss
Im FPT-1000 von Cutmetall Recycling Tools Germany sind derzeit insgesamt 18 Paletten mit unterschiedlichen Höhen. Die Vorrichtungen für die Werkstückaufspannungen befinden sich alle auf den Maschinenpaletten und verbleiben auch dort. In der Regel sind immer die gleichen Werkstücke bzw. Bauteile auf einer Palette. Für die Mehrseitenbearbeitung werden die Werkstücke nach OP10 für OP20 auf derselben Palette umgespannt. „Kommt eine Palette aus dem FPT, haben wir stets eine gewisse Anzahl an Fertigteilen nach OP20 und eine bestimmte Anzahl an Rohteilen für die OP10-Aufspannung, während wiederum andere Teile nach der Erstseitenbearbeitung umgespannt werden. Die Bearbeitungszeiten pro Palette bewegen sich hierbei zwischen 30 und 90 Minuten“, so Fischer.
Produziert wird in zwei Schichten täglich, wobei das automatisierte System zusätzlich unbemannt in einer Nachschicht läuft. „Da die Späneabfuhr in solchen Zeiten das größte Problem darstellt, werden wir zukünftig die Späne aller Maschinen automatisch in eine große zentrale Containermulde transportieren“, meint Fischer.
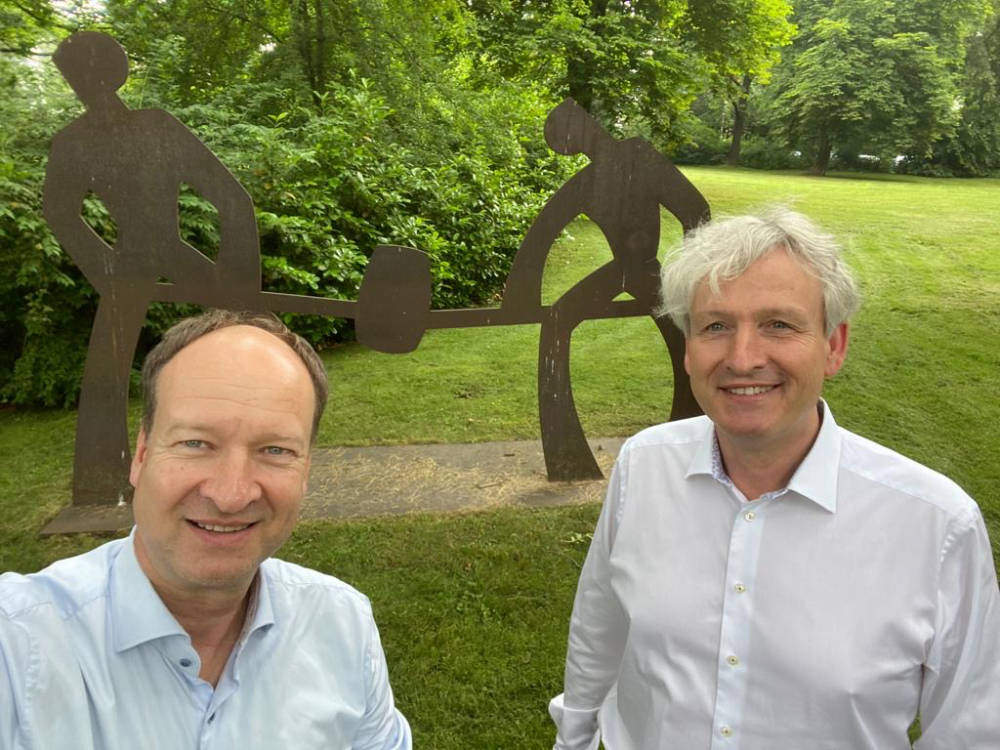
Auf ganzer Linie ein immenser Erfolg
Mit seinem F1-Projekt hat das Unternehmen seine ersten entscheidenden Ziele erreicht. Das zukünftige Automatisierungssystem mit mehreren Maschinen wird das Unternehmen daher schnellstmöglich hochfahren und produktiv einsetzen können, anstatt Monate an Zeit zu investieren, um die gewünschte Auslastung zu erhalten. „Mit dem F1-Projekt haben wir bereits über 7.000 Automatisierungsstunden pro Jahr erreicht, mit einem Anteil von 90 Prozent an Spindelstunden und 10 Prozent für den Paletten- und Werkzeugwechsel. Für uns als mittelständisches Unternehmen mit vergleichsweise kleinen Stückzahlen sind hohe Investitionen etwas ganz Besonderes und angesichts der Tatsache, dass wir die Maschinen nun auf mehr als 7.000 Stunden per annum abschreiben können, ist das ein immenser Erfolg.“